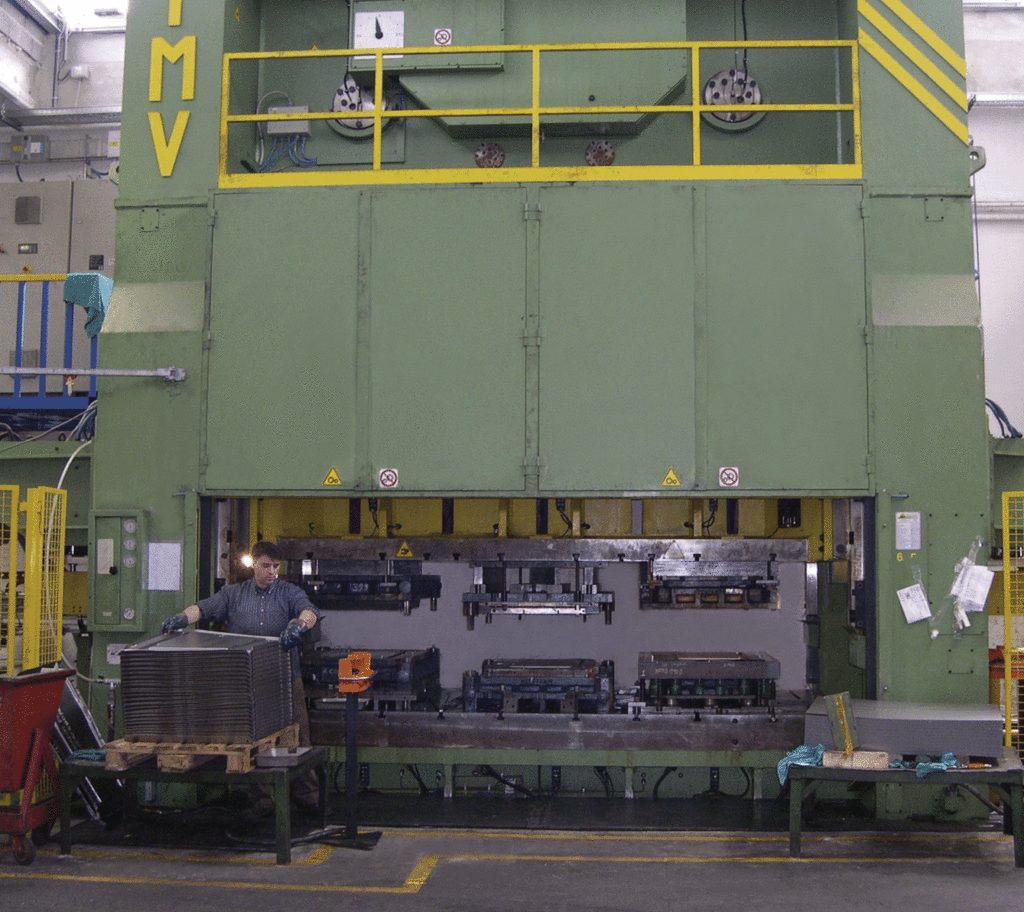
Che spettacolo con le presse!
Senza voler nulla togliere alle altre degne rappresentanti della deformazione non c’è come vedere all’opera una gigantesca pressa per imbutitura per rimanere a bocca aperta. Sì, perché osservare un foglio di lamiera trasformarsi, in un batter di ciglia, in un elaborato pezzo tridimensionale sembra proprio una magia. Uno spettacolo che si ripete ogni giorno nella ditta visitata nel modenese.
Dall’intervista della rivista “Lamiera”.
Mario Palmisano
Cominciata prestissimo, la lunga carriera professionale di Sergio Giugni, classe 1955, presidente della Laroy S.r.l. di San Damaso (MO), è tutta all’insegna della lamiera. A 14 anni, infatti, è già al lavoro fra presse e trance; a 16, nell’azienda del cognato, anch’essa nel settore della deformazione, ha il ruolo di responsabile produzione e a 19 entra nel novero degli imprenditori avendo aperto, insieme ad un socio, un’attività in proprio come stampatore. Due, in particolare, sono le qualità che non si può non attribuirgli, conoscendo il suo percorso: passione e tenacia. Pregi che ha dovuto mettere in campo per vincere quella che forse, finora, è stata la sfida più dura della sua vita lavorativa: realizzare, con l’ausilio della sua più potente pressa oleodinamica, una 1.200 tonnellate, la complessa carcassa di un tosaerba.
Sig. Sergio, la domanda su quella importante scommessa vinta è d’obbligo. Ci vuole fornire qualche informazione in più in proposito?
Partirei col dire che il committente, la Viching del Gruppo Sthil, si è rivolto a noi dopo che altri grossi stampatori europei e cinesi avevano fallito. Il compito era così gravoso che me ne sono occupato personalmente dedicandoci la bellezza di quattro mesi, durante i quali ogni giorno, con ostinazione, ho eseguito prove su prove, con diversi materiali, fino a che dalla speciale pressa, fatta costruire ad hoc, quella carcassa non ne è uscita senza una grinza né un’ondulazione, come il cliente esigeva. Ancora oggi di quel particolare, formato con lamiera DC07 di 1,8 mm di spessore, nelle sue due versioni, una piccola e l’altra grande, ne realizziamo circa 100mila esemplari all’anno.
Con le lamiere, invece, più sottili da voi impiegate, cioè quelle da 0,2 mm che genere di pezzi stampate?
Il prodotto più significativo è destinato al settore automotive ed è un paracalore in alluminio usato per proteggere componenti della vettura a stretto contatto con la marmitta catalitica i cui scarichi arrivano a temperature di 800 e più gradi centigradi. Anche di questo particolare, di cui “sforniamo” qualche milione di pezzi all’anno, siamo molto fieri perché nasce da una tecnologia di trasformazione generata al nostro interno.
Per il buon esito di commesse simili a quelle illustrate, ma anche di altre, magari, meno impegnative, è più importante la pressa o lo stampo?
Non si può dare una risposta precisa a questa domanda. Diciamo, comunque, che per noi ciò che viene prima di tutto è il progetto complessivo riferito ad un ordine, il quale deve tener in debito conto tutti gli elementi riguardanti l’ordine stesso, ed in particolar modo il numero dei pezzi da eseguire. Mi spiego meglio: quando le commesse riguardano pezzi per auto come Ferrari, Lamborghini o Maserati, di cui si propongono poche migliaia di unità all’anno, non conviene certo far costruire stampi da milioni di euro; spesa che, al contrario, stiamo affrontando per la realizzazione del musetto del nuovo Posche Cayenne, la cui tiratura annua prevista, per almeno due lustri, è di circa 150.000 pezzi per un fine vita prodotto di 1.000.000 di pezzi. E, ovviamente, le stesse considerazioni, più o meno, si fanno sulla pressa.
A proposito di presse, protagoniste assolute, nei vostri stabilimenti, ne avete un piccolo esercito, non è vero?
Beh, ci difendiamo bene, per l’esattezza, sono 20: 14 meccaniche, da 15 a 800 tonnellate, e 6 oleodinamiche, da 100 a 1.200 tonnellate. Lo stampaggio viene eseguito manualmente, mediante operatore, o in modo automatico. Per la produzione automatizzata ci serviamo di linee da coils per stampi progressivi, sia con auto bracci e presse a cascata allineate, sia con transfert. Disponiamo, inoltre, di due centri di taglio laser CO2, uno 2D da 1.500 Watt e l’altro 3D da 3.500 Watt, di una pressopiegatrice oleodinamica 60 t x 2.000 mm a 4 assi motorizzati, di una cesoia, di una rifilatrice, di una bordatrice, di una calandra, di puntatrici a proiezione e a colonna e di un’isola di saldatura robotizzata con doppio tornio orbitale a 6 assi.
“Caratterialmente”, per così dire, in cosa differiscono la presse meccaniche da quelle oleodinamiche?
Sono due tecnologie molto diverse, ma entrambe, per essere governate al meglio, richiedono tantissima esperienza. Quella dal carattere più intransigente, però, è senza dubbio la pressa meccanica la quale, a differenza della versione oleodinamica, non ti permette nessun errore nel set up: basta, infatti, commetterne anche uno solo nella regolazione in altezza di uno stampo e la macchina si blocca, con conseguenze spesso disastrose.
Lei è alquanto rammaricato nel constatare che la tecnologia dell’idroformatura non abbia preso piede. Può spendere due parole in proposito?
Già, questa è proprio una nota dolente che chiama in causa i progettisti diretti, cioè quelli in forza alle grandi industrie produttrici di automobili, elettrodomestici e così via, i quali, a causa della loro scarsa, se non del tutto assente, conoscenza di questa rivoluzionaria tecnologia la ignorano, bloccandone così lo sviluppo. E pensare che con una pressa per idroformatura si potrebbero ottenere sottosquadri e forme complesse in tempi brevissimi e con risultati estetici fantastici, oggi ottenibili, invece, con processi tradizionali che prevedono molti più passaggi e dunque tempistiche parecchio più lunghe.
In genere si dice che la qualità è riuscire a fornire al cliente un prodotto che soddisfi la sua richiesta, lei è d’accordo?
No, per me la qualità è il soddisfacimento delle mie necessità, che sono quelle di conoscere perfettamente i materiali e gli strumenti tecnologici di cui facciamo uso, di rendere più efficiente il nostro sistema produttivo e di tenerlo sempre sotto controllo affinché i valori dei ppm non superino lo 0,2, con questo, si va incontro anche all’esigenza, necessità del cliente che lo rende certamente soddisfatto. Già perché con certi clienti se oltrepassi questa soglia nel giro di due giorni vieni cancellato.
Che strategia adottate per distinguervi dalla concorrenza, sempre più agguerrita nel mercato globale?
Il nostro approccio con un potenziale cliente si basa sulla massima trasparenza: quando riceviamo una sua richiesta di offerta gli trasmettiamo una dettagliata “scheda costi” nella quale potrà trovare tutte le voci di spesa che dovremo affrontare per la realizzazione del suo prodotto, unendo altresì alla stessa gli utili che vogliamo ottenere. Ed è così che abbiamo acquisito l’ultimo, importante cliente, il quale, senza nemmeno chiederci un centesimo di sconto, ci ha proposto una mole di lavoro tale che farebbe aumentare il nostro fatturato annuo di 5-6 milioni di euro, cosa, per il momento, al di sopra delle nostre potenzialità.
Nel momento in cui lascerà il timone della Laroy, che realtà le piacerebbe lasciare ai suoi figli, già al suo fianco da parecchi anni?
Il mio desiderio sarebbe quello di consegnarli un’azienda con spazi maggiori che permettano una più razionale esecuzione della produzione, anche sotto il profilo logistico. In essa poi sogno di vedere all’opera una nuova pressa meccanica da 1.500 tonnellate. Con un tale ulteriore “gigante” a disposizione avremmo di sicuro una marcia in più.