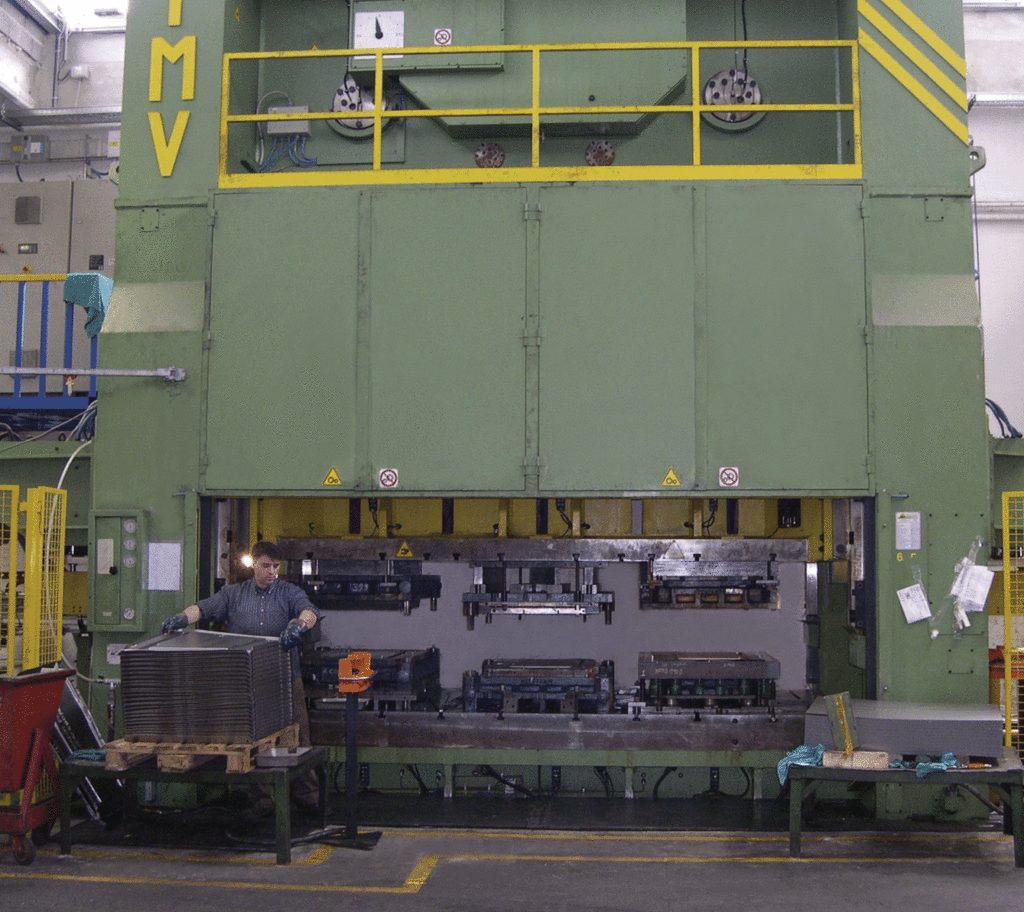
THAT SHOW WITH PRESSES!
Without wanting to take anything away from the other worthy representatives of the deformation, there is no way to see a gigantic drawing press at work to keep your mouth open. Yes, because watching a sheet of metal turn into a blink of an eyelid, in an elaborate three-dimensional piece it looks like a magic. A show that is repeated every day in the company visited in the Modena area.
From the interview of the magazine “Lamiera”.
Mario Palmisano
Started soon, the long professional career of Sergio Giugni, born in 1955, president of Laroy S.r.l. of San Damaso (MO), it is all in the name of sheet metal. At 14, in fact, he is already at work between presses and trances; at 16, in the company of the brother-in-law, also in the deformation sector, has the role of production manager and 19 enters the group of entrepreneurs having opened, together with a partner, a business in its own as a printer. Two, in particular, are the qualities that can not be attributed to him, knowing his path: passion and tenacity. He had to put in place to win what perhaps, until now, was the hardest challenge of his working life: to build, with the help of his most powerful hydraulic press, a 1,200 tons, the complex carcass of a lawnmower.
Mr. Sergio, the question about that important bet won is a must. Do you want to provide some more information about it?
I would start by saying that the client, the Viching of the Sthil Group, turned to us after other big European and Chinese printers had failed. The task was so heavy that I took care of it personally, dedicating the beauty of four months, during which, every day, with obstinacy, I performed tests on tests, with different materials, until the special press, built ad hoc, that carcass did not come out without a wrinkle or a ripple, as the customer demanded. Even today of that particular, formed with DC07 sheet of 1.8 mm thick, in its two versions, one small and one large, we make about 100 thousand copies a year.
With the sheets, however, thinner than you used, ie those of 0.2 mm that kind of pieces printed?
The most significant product is intended for the automotive sector and is an aluminum heat shield used to protect components of the car in close contact with the catalytic converter whose discharges reach temperatures of 800 and plus degrees Celsius. Also of this particular, of which “we churn” a few million pieces a year, we are very proud because it comes from a technology of transformation generated within us.
For the success of orders similar to those illustrated, but also others, perhaps less demanding, is the press or the mold more important?
We can not give a precise answer to this question. Let’s say, however, that for us what comes first of all is the overall project related to an order, which must take into account all the elements concerning the order itself, and in particular the number of pieces to be executed. Let me explain: when the orders are for car parts such as Ferrari, Lamborghini or Maserati, of which only a few thousand units are offered per year, it is certainly not convenient to build molds for millions of euros; on the contrary, we are dealing with the construction of the new Posche Cayenne’s nosepiece, whose expected annual circulation, for at least two decades, is about 150,000 pieces for a product end of 1,000,000 pieces. And, of course, the same considerations, more or less, are made on the press.
Speaking of presses, absolute protagonists, in your factories, you have a small army, do not you?
Well, we defend well, to be exact, are 20: 14 mechanical, from 15 to 800 tons, and 6 hydraulic, from 100 to 1,200 tons. The molding is performed manually, by operator, or automatically. For automated production we use coils lines for progressive dies, both with self-arms and aligned cascade presses, and with transfer. We also have two CO2 laser cutting centers, a 1,500 Watt 2D and the other 3,500 Watt 3D, a 60 tx 2,000 mm hydraulic press brake with 4 driven axles, a shear, a trimming machine, a beading machine , of a grille, of projection and column pointers and of a robotized welding island with double 6-axis orbital lathe.
“Characteristic”, so to speak, in what do the mechanical and oleodynamic presses differ?
They are two very different technologies, but both, to be governed at best, require a lot of experience. The one with the most intransigent character, however, is undoubtedly the mechanical press which, unlike the hydraulic version, does not allow you any error in the set up: it is enough, in fact, to commit even one in the height adjustment of a mold and the machine it stops, with often disastrous consequences.
You are somewhat regretted to see that the hydroforming technology has not taken hold. Can you spend two words about it?
Already, this is just a sore point that calls into question the direct designers, that is those in force to large industries producing cars, home appliances and so on, which, because of their scarce, if not completely absent, knowledge of this revolutionary technology ignore it, thus blocking its development. And to think that with a hydroforming press you could get undercuts and complex shapes in a very short time and with fantastic aesthetic results, nowadays obtainable, instead, with traditional processes that involve many more steps and therefore a lot longer timeframes.
It is generally said that quality is being able to provide the customer with a product that meets his request, do you agree?
No, for me quality is the satisfaction of my needs, which are to know perfectly the materials and technological tools we use, to make our production system more efficient and to keep it under control so that the ppm values do not exceeding 0.2, with this, we also meet the need, the need of the customer that certainly makes him satisfied. Yes, because with some customers if you cross this threshold within two days you are canceled.
What strategy have been adopted to distinguish you from the competition, increasingly fierce in the global market?
Our approach with a potential client is based on maximum transparency: when we receive an offer request we send you a detailed “cost card” in which you will find all the items of expenditure that we will have to face for the realization of your product, also joining the same as the profits we want to get. And that’s how we acquired the last, important customer, who, without even asking us for a hundredth of a discount, offered us a workload that would increase our annual turnover by 5-6 million euros, what, for the moment, above our potential.
The moment you leave the helm of the Laroy, what reality would you like to leave to your children, already by your side for several years?
My desire would be to deliver a company with larger spaces that allow a more rational production, even from a logistical point of view. Then I dream of seeing a new 1,500-ton mechanical press at work. With such a further “giant” available we would certainly have an extra gear.